热处理托盘应对货物倾斜堆叠的解决方案
在高温热处理场景中,托盘需同时承受货物重量和热应力,倾斜堆叠易引发货物滑移、设备损伤甚至安全事故。针对此问题,需从结构设计、操作规范及辅助措施三方面进行系统性优化。
一、托盘结构强化设计
1. 底部支撑优化:采用X型或网格状加强筋结构,提升纵向承重能力,防止高温软化导致的形变。金属托盘推荐使用耐热合金钢(如310S不锈钢),其高温强度比普通钢材提升40%以上。
2. 防滑表面处理:表面采用凹凸纹路设计或喷涂碳化硅涂层,摩擦系数可达0.6-0.8,较光滑表面防滑性能提升3倍。边缘设置15°倾角的防溢挡板,有效限制货物位移。
3. 标准化定位槽:根据典型工件尺寸设计嵌入式卡槽,如轴承类零件采用环形凹槽,使货物始终位于托盘几何中心±5cm范围内。
二、堆叠操作规范
1. 分层控制:制定不同物料的堆叠高度标准,如铸件不超过4层(总高≤1.2m),薄板件采用交叉堆叠法,每层旋转15°以增强稳定性。
2. 管理:重物下层原则执行误差不超过5%,单件超过50kg的工件需单独配置配重块。采用激光水平仪实时监测堆垛倾斜度,确保角度偏差<3°。
3. 热胀冷缩补偿:预留2-3mm/米的膨胀间隙,高温工况下使用陶瓷纤维垫片隔离层间接触面。
三、辅助固定系统
1. 智能绑扎装置:配置耐高温(≥800℃)的Inconel合金锁扣,配合自动张紧系统,可承受2000N的横向拉力。RFID标签实时监测绑带张力,偏离设定值15%即触发警报。
2. 模块化分隔架:可拆卸式钛合金隔板系统,通过燕尾槽结构快速组装,单隔板承重达150kg。配置红外定位传感器确保隔板对齐精度±1mm。
3. AGV联动系统:堆垛完成后由AGV自动扫描坐标,通过算法优化运输路径,将加速度控制在0.3m/s²以内,减少动态倾斜风险。
实际应用案例显示,某汽车零部件厂通过综合运用上述方案,使热处理环节的货物倾斜事故率从7.3%降至0.5%,托盘使用寿命延长至1800次热处理循环。建议企业定期进行三维力学校核和热变形模拟,结合MES系统实现堆叠参数的动态优化。
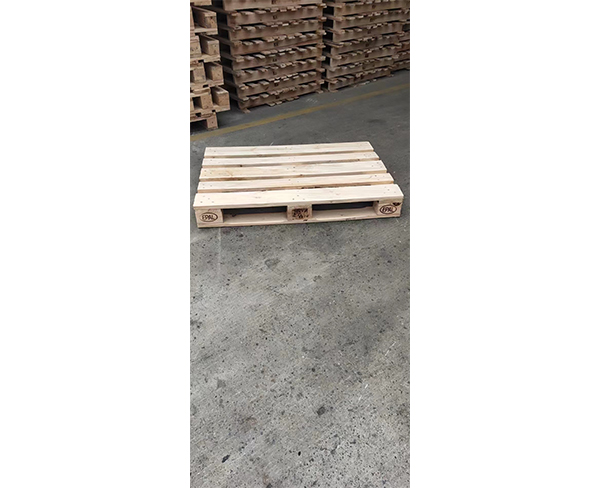
上一条:热处理托盘的生产周期能否缩短?
下一条:热处理托盘在高温环境下稳定吗?